The Value for Oil & Gas Companies to Standardize on Single-Source Seals
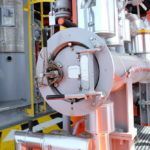
Procurement for oil and gas projects has become very complex due to growing size, lethal environments, and demanding regulations.
Many oil & gas companies now split projects into multiple EPC (Engineering Procurement & Construction) contracts. This can naturally lead to mixing 10 or so different manufacturers’ products with disparate materials and specifications even though they come under the same industry standard.
In an industry where safety and performance are critical, this creates a potential quagmire of unmanageable complexity that risks cost-effectiveness, production loss, infrastructure damage, and injuries.
Consistent quality and integrity assuring performance
Multi-sourcing on critical asset components, such as mechanical seals, can compromise the safety of a whole project. Without oil & gas companies carrying out their own rigorous checks through the project, there is no way of knowing that fittings are fully tested and guaranteed to work together.
A transparent collaborative contract with a single-source supplier (for each range of components such as seals) means all parties including sub-contractors are clearly focused on delivering a robust solution that’s compliant to specified requirements.
Consistent standard testing and documentation is taken care of, providing extra reassurance and peace of mind for the oil and gas operator.
Tailored solutions with complete service
A single-source supplier takes greater ownership of a project, providing a completely integrated, dedicated, and comprehensive service––making life simpler and safer for the end client.
Saving on inventory management
It is challenging for end clients to keep track of the components that are being installed on their sites, especially over wide geographical areas.
A major benefit of single-sourcing for the end client is simpler stock management. It helps the client to reduce the risk of mixing different manufacturers’ components on site as well as keeping stock levels down––making operations more cost-effective in the long term.
Economy of scale bringing costs down
By supplying a larger volume of components, suppliers can deliver a more cost-effective solution for the oil and gas operator.
Getting the best results for oil and gas projects
As a single source for seal components, Eclipse can offer oil & gas clients the very best value, assured performance, consistent standards, and minimized risk of production loss, infrastructure harm, and safety breaches.
Find out more about what Eclipse can do for the oil & gas industry , with distribution of a wide range of perfect-fit mechanical seals including o-rings and gaskets.
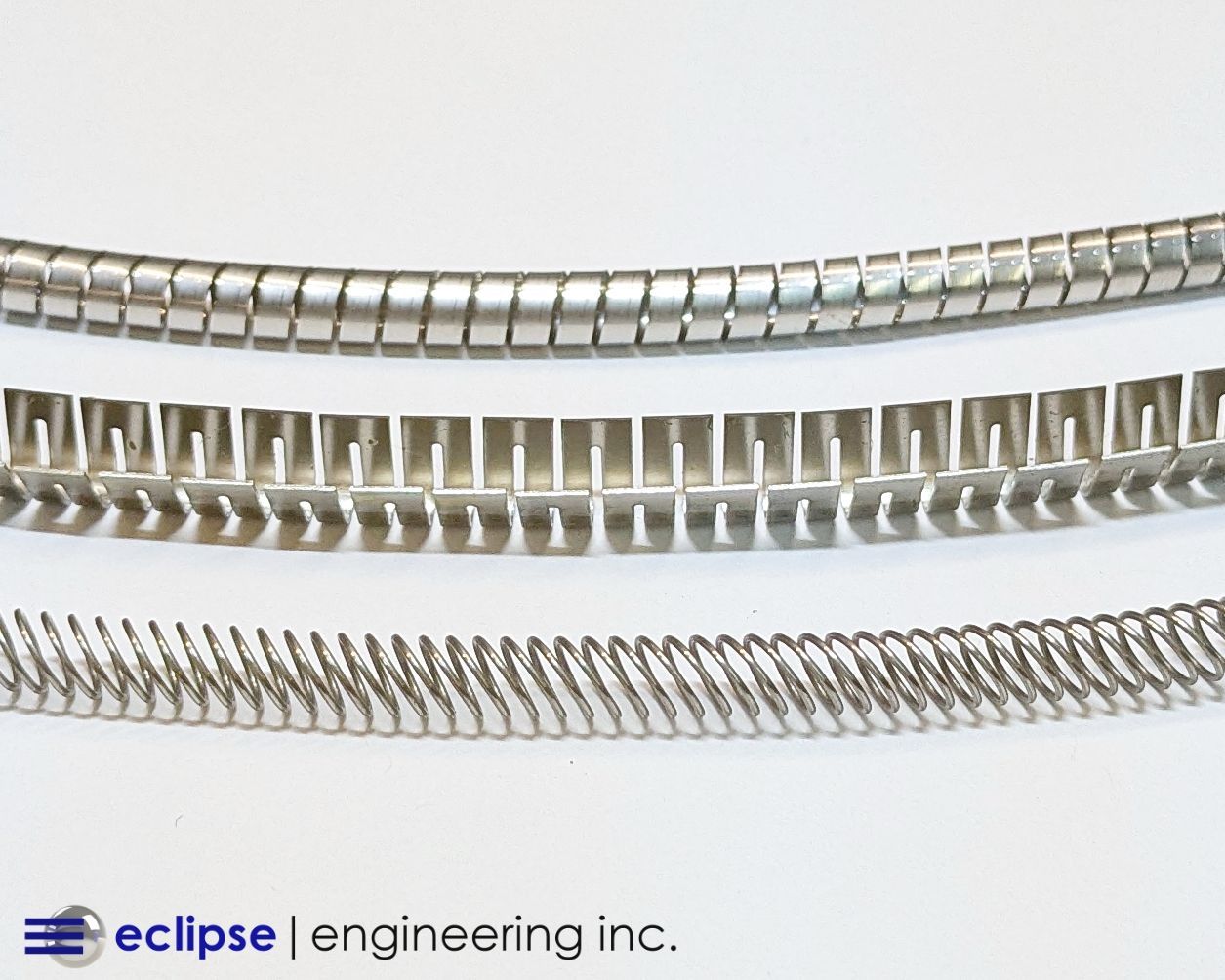