The Advantages of a Canted Coil Spring Energizer
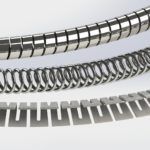
When considering polymer jacketed seals — especially PTFE-based products — some form of energizer is typically required. These types of seals are usually specified to operate both in very high pressures, low pressures, or even in a vacuum.
At some pressure (typically above 100psi), the system pressure will energize the seal and prevent leakage. But at low pressures, additional energy is required to force the jacket material to mate with the hardware.
The solution to this is to add a spring to the seal. The spring provides the needed sealing-energy to prevent leakage at low media pressures.
When considering a high pressure-application, there are start/stop conditions where the system is at low pressure. If the seal allows some amount of leakage at low pressure, it becomes possible for that leakage level to increase once as the pressure builds.
This phenomenon is called “blow-by.” Once it occurs in a system, it’s difficult to get the seal to seat and seal correctly.
Canted Coil Spring Energizer
There are several types of energizers to consider when specifying a seal. These can be as simple as an O-Ring or some other elastomer.
We most often recommend a metal energizer such as a garter, cantilever, helical, or canted coil spring. The canted coil spring offers some very interesting properties that other springs don’t display.
Once the canted coil spring begins to be deflected, it has a relatively flat force curve in the middle of its travel. This allows the designer to have a consistent load over a very broad deflection range.
This spring type is also resistant to damage unless it’s stretched. Unlike cantilever v-spring or helical spring which can be yielded and take a set when over-compressed, the canted coil is almost impervious to this. A hard stop will be reached once the coils are “butted” preserving the spring functionality.
Canted Coil in Seals
In seals, the canted coil spring is used to force the lips of a polymeric or elastomeric seal out. This causes the seal to always be in contact with the sealing surface supplying contact force for low pressure sealing.
Another key factor is the ability to control the load where friction forces need to be kept to a minimum. As the seal wears, with a relatively flat load curve, those friction forces will remain at the desired level throughout the life of the seal.
Eclipse designs and constructs all the necessary fixturing and tools to facilitate the cutting and welding of canted coil spring for use in seals. Eclipse takes no shortcuts in seal manufacturing as all our springs are fully welded before being installed in any seal.
Our canted coil is welded using our state-of-the-art laser welder ensuring a very small, accurate, and strong weld.
Canted Coil in Detent Mechanisms
Another aspect of canted coil spring is its advantages in detent mechanisms. This is very useful where a reusable lock is required between two moving components.
A groove is machined in both parts, and the energy of the canted coil retains and soft locks the parts together. This allows for nearly limitless lock / unlock cycles to be possible.
Canted Coil and EMI Shielding
The canted coil spring can also be used to create EMI (Electro Magnetic Interference) shielding between two metal components. With a change in material, these springs can create the type of shielding necessary to reduce or eliminate EMI from other sensitive electronic circuits in a piece of equipment.
A variation of this is using a canted coil as an electrical conduit where coupling connections needs to be made.
Metallic energizers can be made from a wide variety of materials. The most common one being 300 series stainless steel.
For chemical resistance, Hastelloy and Elgiloy are commonly found in the oil drilling applications to handle high heat and Hydrogen Sulfide, a highly corrosive gas.
Eclipse Excels at Energized Seals
Eclipse Engineering has been manufacturing elastomeric and metal spring energized seals for over 20 years. With our ability to create tools in house, we have the capability to manufacture seals that are under 1/16 inch up to in excess of 50 inches in diameter.
Creating custom springs including photo-etched cross section springs are all available to the designer today at relatively low cost even for short runs. Learn more about our canted coil spring seals >
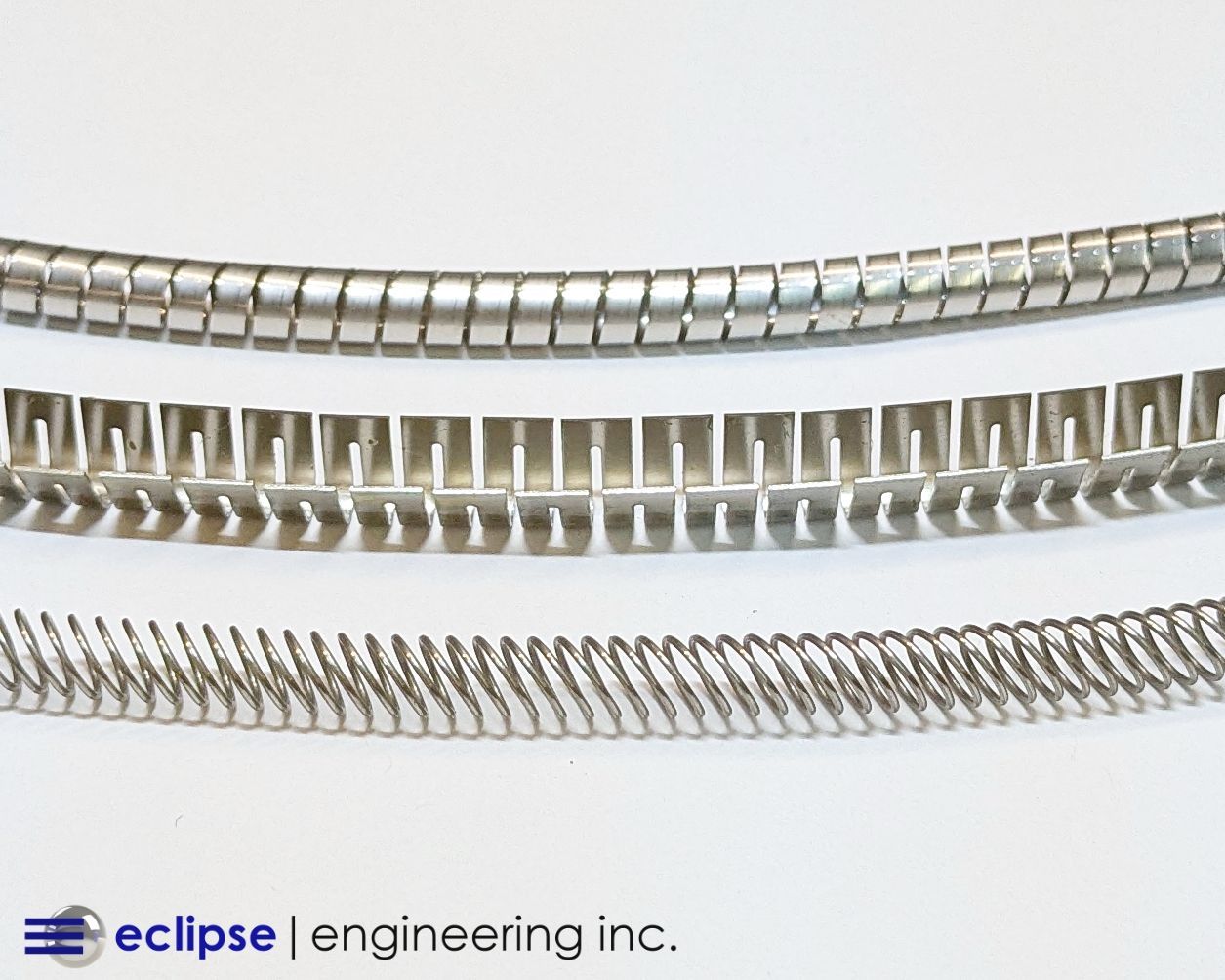